How nuclear reactors are made
Production process
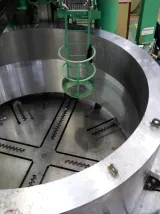
Metallurgical blanks for the reactor pressure vessel are supplied from AEM-Special Steels Plant. Large-sized workpieces undergo incoming inspection, vertical lathe machine working of surfaces and edges for welding. After inspection job, the workpieces enter on the further process steps: assembly and welding.
A pearlitic steel slab is preheated in a furnace at a temperature of 1000 °C and then it is placed under max 15000 ton-force press, which forms a head of the slab. The double-acting hydraulic sheet-metal stamping press is unique and Russia’s only equipment that can stamp heads of a slab up to 380 mm thick.
In total, hundreds operations are carried out after jointing of the reactor half-vessels. Particular attention is paid to non-destructive testing methods.
768
110
4900
The equipment is delivered to the factory berth by special vehicles. Self-propelled and tractor-driven modular multi-axle trawls are used, which are capable of withstanding a load of over 400 tons. Loading operations are carried out using two cranes with a lifting capacity of 650 tons each.